
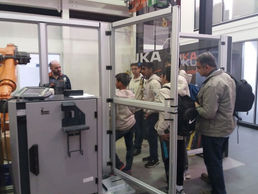
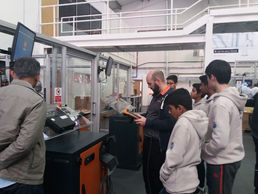





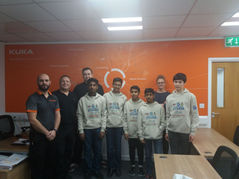

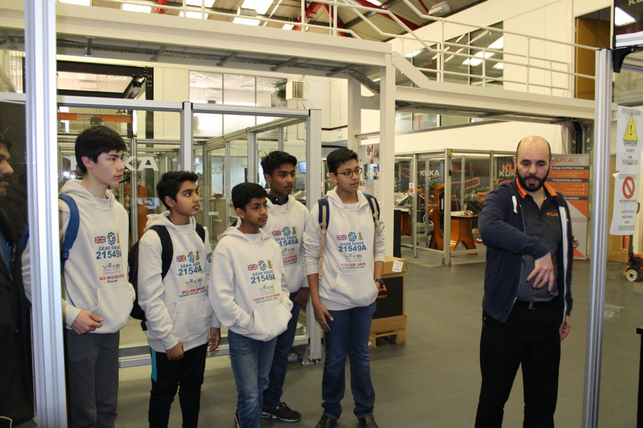
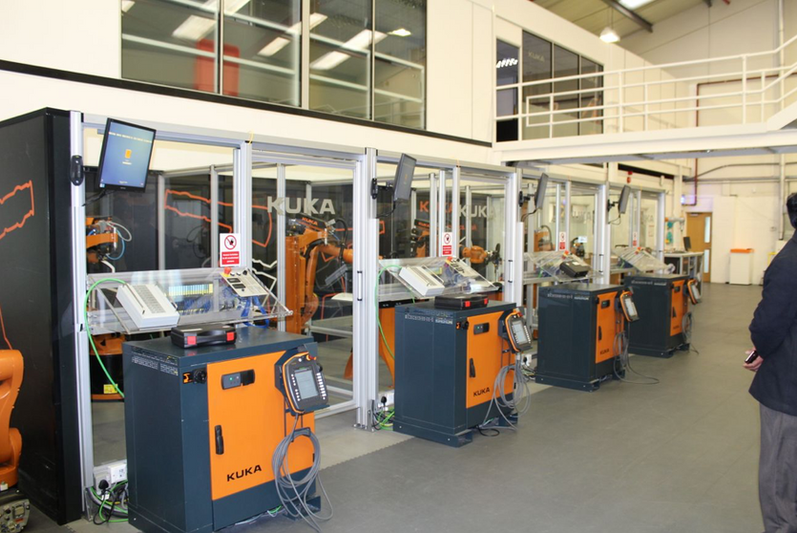
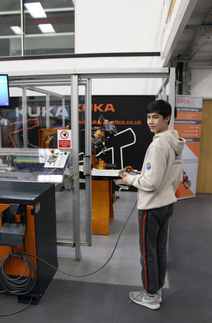

A DAY OUT
On Friday 19th January, we were fortunate enough to be invited to the KUKA factory in Wednesbury and what a day that was!
It all started when we emailed KUKA, requesting for sponsorship for our team. The reply that we received was shocking for us. Not only were they perfectly delighted to sponsor us, they invited us to their factory in Wednesbury. Initially, they planned the visit on the 26th of January, but after we found out that our Henrietta Barnett regional competition was on that date, we emailed them to change it; they moved the visit to the week before (on the 19th). KUKA told us to that we should be at their factory at 10am and that we would leave their factory at 4pm. This got us wondering, about what we were going to do for those 6 hours and made us even more excited. Travel arrangements were made very quickly, for Shilacshan’s father was able to take us, for he had a vehicle that was capable of carrying 6 passengers. This meant that as well as the five of us, one other person (apart from Shilacshan’s father) was able to come, so Dillan’s father came with as well. Since, it was a school day, we had to ask for permission from the school to have an absence. The school had happily granted the absence for it was educational. There was nothing stopping us from going now…
Eventually, the excitement was over, as the day of the trip had arrived. All 5 members of the team, as well as Shilacshan’s father and Dillan’s father, arranged to meet up at Dillan’s house as it was the most convenient for all of us. After we met at Dillan’s house, we set off on our journey to the KUKA factory.
We left Dillan’s house at 7.30am and were expected to arrive at the KUKA factory at 10am. The journey was very long; 113 miles and, was two and a half hours long!
At 9.45am, we arrived at the factory. The factory was not hard to find, and we knew that we had arrived at the correct place due to the two robotic arms in front.
We walked into the reception and were immediately recognised by the receptionists – perhaps our team jumpers gave ourselves away. We met Steve, who was with us for the entire day (as well as other people). He showed us to our refreshment area, via the main factory area, and we all caught a glimpse of many autonomously working robots.
After a quick drink and a snack, Steve led us towards a robot. It was unlike the other robots. Whilst the other robots were bright orange (the colour of the KUKA logo), this one was white. Steve explained how this robot was a medical robot, designed for medical purposes. For that reason, the robot was gentle and smooth for it has to work with humans. It was safe for people to touch the robot. Unlike, the other, older robots, this robot was made up of predominantly plastic and the metal used was aluminium. We were eager so see it working, but Steve told us that some people were coming that afternoon and, he said that he must not move the robot for there was an autonomous program which he did not want to disrupt.
Next, we were lead to larger, orange robots. These were the sort that were used in factories and, were quite large; there was more metal (magnetic metals) on these robots than the medical robots. At this robot, Steve showed us how the control system works. The was a device, similar to a tablet, that was used as a remote control. However, it was not wirelessly connected to the robot. There was a box, which was needed for the robot to work, to which the controller was connected to. It had a battery, hard drive, and other parts similar to that of a computer. We compared this to a VEX IQ robot brain. These parts are apparently not made by KUKA itself, but smaller companies it has contracts with, which shows that even large companies need the smaller, less well-known companies to function. When, we asked why the remote was not wireless as surely that would have been easier, Steve stated that it was for safety. He said that a wireless connection was not always going to work and, if you need to turn the robot off for an emergency, the wireless could not work. With a wired connection, the controller is always connected to the robot which would be more reliable when it comes to telling the robot to cease.
Then, we were led to a room that looked like a mini classroom or some sort of room you would expect to have formal meetings in. In here, Steve taught us about how the robot works, (basic explanations) and how to control the robot. We learnt that there are six axes that cause the robot to turn. We also learnt about ways of moving the robot arm. One way that we could do that is by rotating each part of the robot around the axes
There are 6 axes on this robot, which can all be moved individually when an axis mode. We were also taught how to use the base mode, this is when the end of the arm is controlled by movement in the X, Y and, Z axis (relative to a base, which was a point on a table, and rotation around those axes, A, B and, C. All members of Gear Squad found this mode easy, although Dillan and Vihaan sometimes changed to axis mode for tricky manoeuvres, whilst Shilacshan, Varun and Alex stuck to base mode. Most importantly, in the room, we learnt about the safety. This included how to stop the robot, as well as being taught what we can touch and what we cannot touch.
During this session, our programmer, Varun, got fascinated by how the programme works. The programming language was called KUKA Robot language (KRL). This is a language unique to KUKA robots which is similar to Pascal. The actual coding is very basic, for complex coding has been shortened to simple sentences, like Robot C.
Now we were ready to try out the robots!
Our first task was to stack some metal cubes, using a claw that was attached to the robot arm. Varun – driver and programmer—found this very easy and stacked 10 blocks before everyone else stacked 5! The problem for most of us, was the speed of the robot and the sensitivity. As the speed was adjustable, most of us put it on a low speed (such as 30). This was because, if the claw hits anything, particularly the table, there would be a loud noise followed by hissing as the claw comes off. If this happens, a member of the KUKA staff have to come over (there was one supervising each person due to safety) and fix it. Initially, particularly for Shilacshan, that noise was disturbing. However, one has to understand that, that procedure was for our safety. When a certain amount of pressure was applied onto the claw, the claw breaks due to hydraulics. This prevents it from breaking the glass that surround the robot.
It was lunch time. The food that we received was better than we thought and all members, including Dillan’s Father and Shilacshan’s Father, enjoyed the lunch. Even the coffee machine was robotic! (therefore, difficult to operate!)
After a magnificent lunch, we resumed with the robots. This time, we focused on autonomous programming. This involved moving a pen over a table, following the lines on it. In order for us to be able to do this, we had to learn about linear movement, point to point movement and circular movement. Linear movement is the quickest movement from one point to another, often using only one axis; it may be in an arc shape. Point to point movement is the straightest route from one point to another. Circular movement is moving in circular shapes which may help to climb up slopes. As a matter of fact, Alex and Shilacshan finished this task before the others and they both tried the next hardest shape whilst waiting for the others to finish.
Now that the team had completed the autonomous control, we had some free time. Alex and Varun tried to programme that robot to stack the cubes, whereas Dillan, Vihaan and Shilacshan wanted to practice their manual control. Alex and Varun managed to successfully program the arm to stack 5 blocks autonomously. Eventually, as our arms ached (as well as time), we finished with the robots. Now we took one last group photo, before receiving our gift bags full of KUKA branded items.
Unfortunately, that was the end of our KUKA trip. We had a wonderful day out with us learning many new things in a fun and enjoyable way. (We also learnt more about each other and our strengths and weaknesses when it comes to operating robotic arms). We hope to experience such a day out again and we would go back to the factory for round two if we had the chance.
We thank KUKA for creating such a brilliant day and we promise that KUKA will be advertised well.
Written by Shilacshan